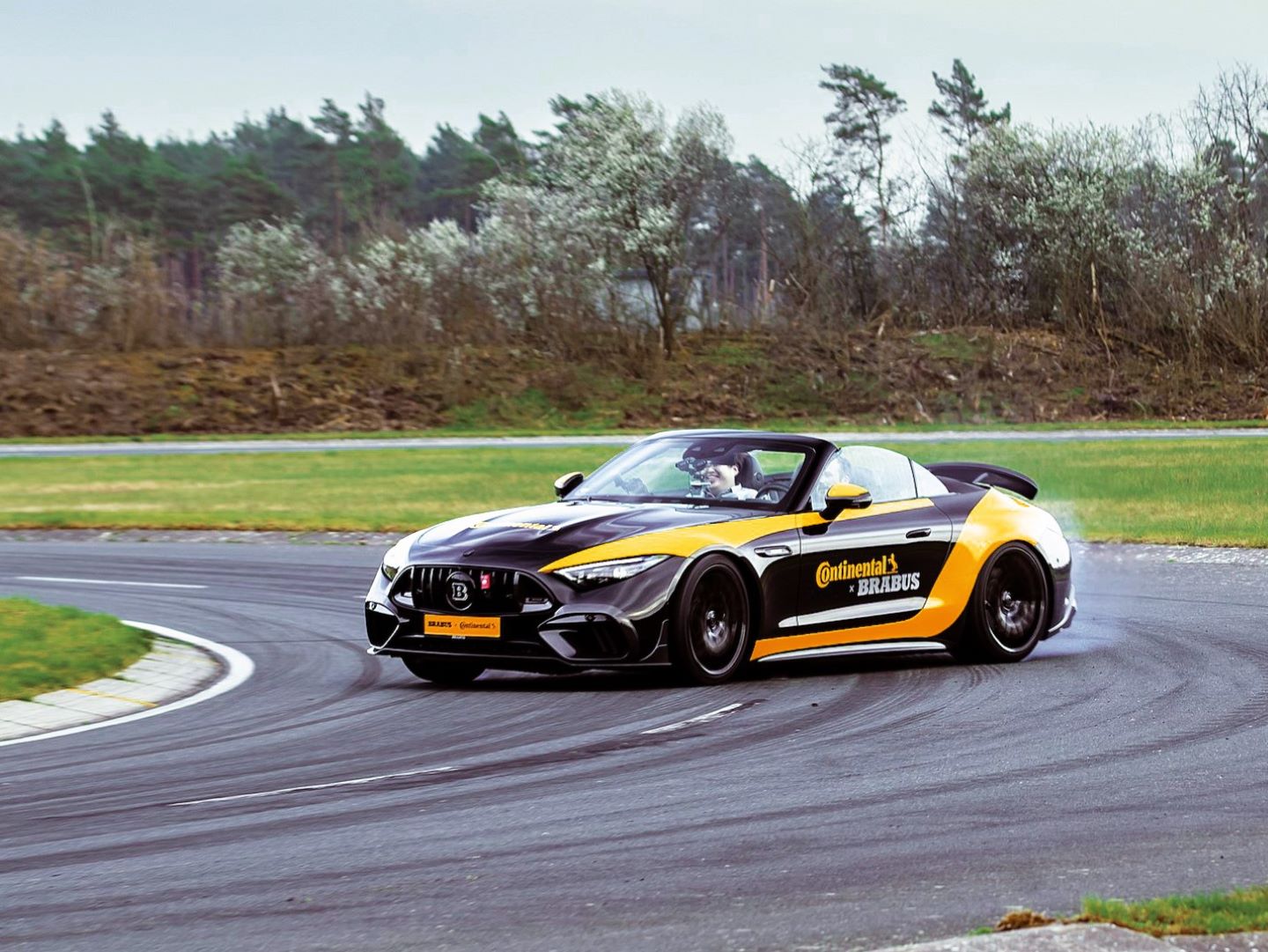
The Brabus 750 Bodo Buschmann smokes its tyres during hard cornering at the Contidrom Dry track during a demonstration run (Photo: Continental Tires and Brabus)
The Brabus 750 Bodo Buschmann is a fitting vehicle to put Continental’s latest high-performance tyre, the MaxContact MC7, to the test. Available in Asia-Pacific exclusively since the first quarter of this year, the MC7 has big shoes to fill, succeeding the highly acclaimed MaxContact MC6.
Continental took an already highly competitive tyre in the MC6 and invested 8,000 hours of research and development in developing the even better MC7.
The vehicle itself is based on the Mercedes-AMG SL 63 4MATIC+ Roadster, customised to a whopping 750bhp, enabling it to reach 100kph from 0 in 3.3 seconds and hit a top speed of 315kph. Other modifications include custom wheels, a reworking of the interior, carbon-fibre body extensions, suspension and exhaust system, to create a limited run of just 25 units for the one-of-a-kind roadster. All units have been pre-sold.
Continental Tires recently hosted a pre-launch of the MC7 at the Contidrom, its tyre test facility in Germany. To take it to the limit, the car was piloted by Lance David Arnold, a German race car driver with a distinguished racing career, who smiled as I hopped into the passenger seat, the interior reeking of leather above the smell of smoking rubber and distressed brake pads hovering in the car after repeated runs.
We were on the test portion of the Contidrom’s 3.8km dry track. Lance asked if I had been on a racetrack before to reassure himself I wasn’t going to throw up halfway and soil the quilted leather seats, before flooring the accelerator and hurtling the car towards the horizon on the straightway.
tyre.jpg
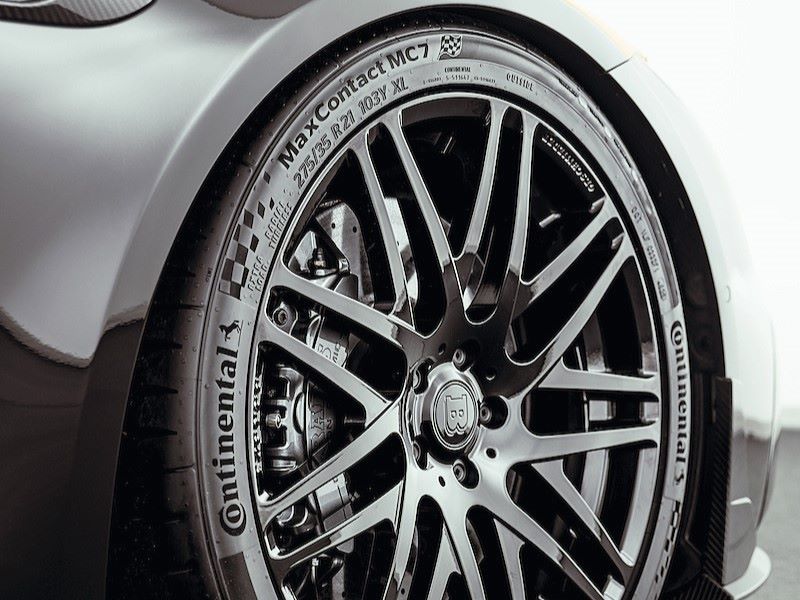
What impressed, besides the absolute control of the driver, pushing the car to the edge in manual transmission mode, traction control disengaged, was the composure of the car, with no stomach-churning yawing or pitching in hard cornering and furious acceleration. There was never the threat of the tail stepping out of line, just reassuring compliance and explosive power out of
the corners.
Such was the aerodynamics that I could speak to Lance without raising my voice, as we hurtled along. Despite the soft top being down, a passenger with a bouffant hairdo would have emerged with puffy, rounded hairstyle unruffled after highly illegal three-digit speeds.
The track, with its sinuous twists, tight turns and straight sections, was an excellent platform to assess the MC7 tyres. They were impressively quiet despite the ferocious speed, the broad contact patch from the squat, low-profile tyres — 275/35 R21 (front), 335/25 R22 (rear) — generating surprisingly little road noise above the boom and roar of the car in full flight.
Even more impressive was the massive grip in hard braking and cornering, for although they squealed mightily when pushed, they never slid off the chosen path. But the stupendous grip was not entirely surprising.
wet.jpg
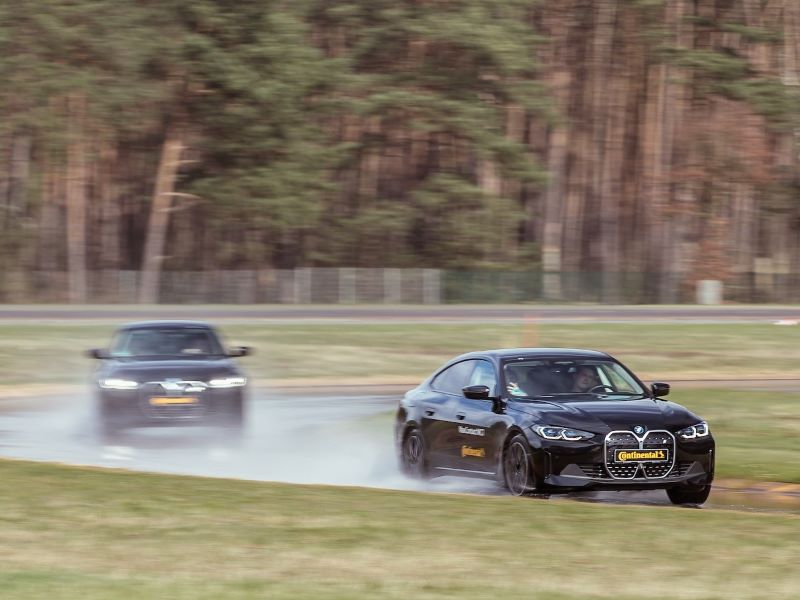
Earlier, I had had the opportunity to experience the tyres first-hand on the wet track of the Contidrom. Two cars had been set up, identical except for the tyres, one fitted with the MC7, and the other, a competitor’s high-performance tyres.
The wet track, continuously watered by sprinklers, was 1.8km of straights, sweeping and tight turns and S-sections. The difference between the two tyres, driven back to back, was massive.
Most evident at low speeds was how quiet the MC7 was compared with the competitor, and the relative compliance of the ride. As speed picked up in succeeding laps, speeds on the MC7 were higher in hard wet braking, acceleration and cornering. Even with traction control, I felt the tail of the car twitching in some of the faster corners on the competitor tyres. By contrast, the MC7 — to use a cliché — handled as if on rails, predictable and controlled, and inspired a good deal more confidence in the wet.
In all areas, the MC7 eclipsed the competitor tyres convincingly. Remarkably, the competitor tyres were not an obscure or unknown make, and have fared quite well in independent reviews.
Testing tyres to the limit
Located 40km from Hanover, in pastoral countryside, the Contidrom has been Continental Tires’ main test centre for tyres since the facility first opened in 1967 with the high-speed cornering oval with banked corners. Astonishingly, over 1.3 million tyres have been tested here and there are extensive testing facilities for aquaplaning, wet and dry handling and braking, summer and winter driving and even off-road conditions for 4WD tyres.
Complementing the outdoor tracks are various facilities, such as the AIBA (Automated Indoor Braking Analyzer), a facility to test braking independent of weather and external temperature conditions. In the 300m-long closed building, driverless vehicles are accelerated automatically and then braked by a robot over driving surfaces that can be changed.
aiba.jpg
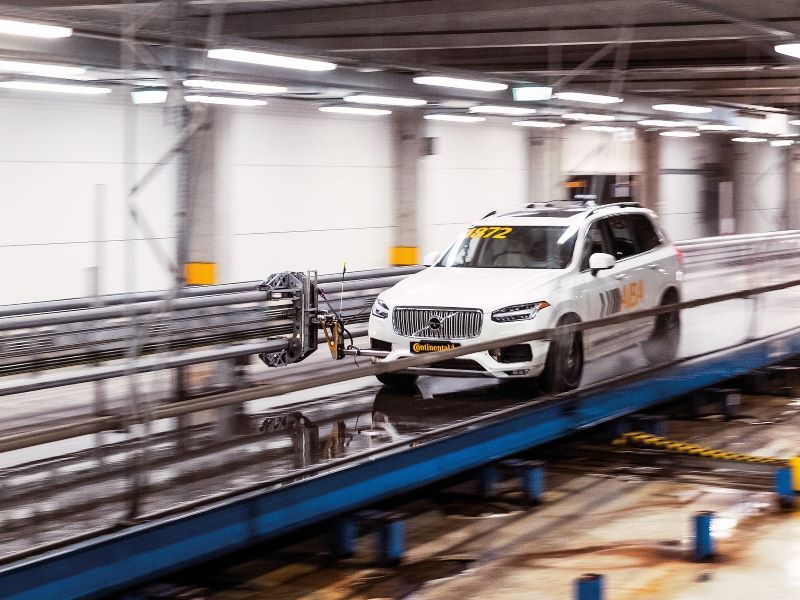
There is a facility with an iced-over indoor track for testing snow tyres. Slip-on rubber shoes soled with summer and winter tyre treads enable observers to appreciate first-hand, the difference in grip between both types of tyres.
Since November 2023, a driving simulator has provided virtual testing for specific tyres in specific vehicles, reducing development times. The driver is seated in a test vehicle robot on moveable arms, facing a wraparound panoramic screen of the high-speed oval. Prototype tyre parameters such as tread pattern and rubber compound are modelled in software and loaded into the simulator.
The simulated driving experience provides instant feedback on tyre dynamics measured through sensors and the driver’s subjective feedback. This process obviates the need to physically test each change in tyre parameter in the real world, dramatically reducing tyre development time and material usage.
Developments in tyre technology can also be directly compared. I drove two test cars, one equipped with the latest ContactSport 7, the other with 20-year-old technology in a newly produced Continental Sport Contact 2, the leading-edge high-performance tyre of its era. The latter was freshly produced using the original rubber compound and tread pattern to eliminate the effects of rubber degradation from ageing.
In repeated emergency braking on a wet track, the current-generation tyre outbraked the other by an average of 3m from 85kph, potentially the difference between avoiding a collision and being in one.
Bespoke high performance
Brabus needs no introduction to Malaysian drivers of high-performance vehicles, particularly Mercedes-Benz. Its exclusivity and independence set it apart from AMG, Mercedes’ own high-performance subsidiary.
Brabus started in 1977 by customising Mercedes-Benz cars — the father of Bodo Buschmann, its founder, was a Mercedes-Benz dealer — and has gone from strength to strength, customising mainly Mercedes-Benz and Smart, as well as Range Rover, Porsche, Rolls-Royce and Maybach cars. Other business lines include classic car restoration, marine (boats), fashion (merchandise) and accessories.
factory.jpg
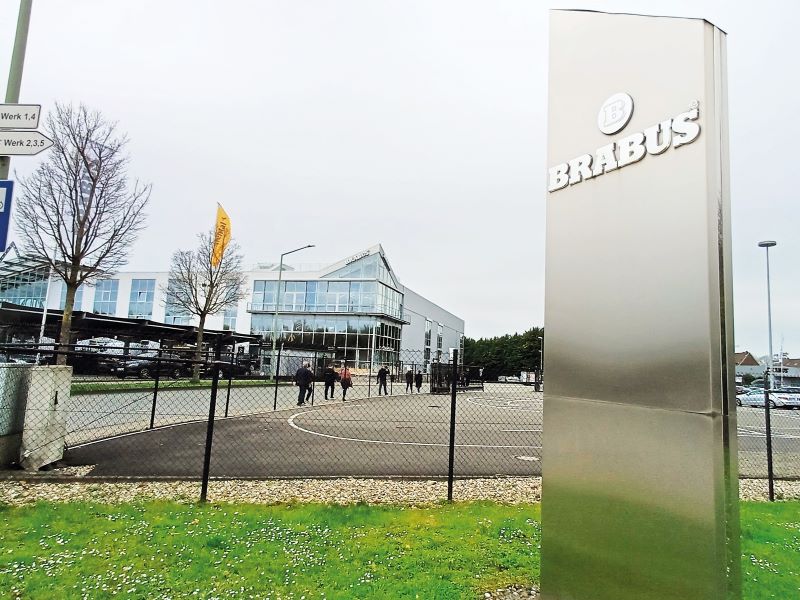
Bottrop, a town about 50km from Dusseldorf, houses Brabus’ factory complex. The reception area is lined with drool-worthy restored classic Mercedes-Benz cars, highlighting the Brabus Classic 6-Star Restoration business line, which sources, restores and sells complete classic Mercedes-Benz cars.
Although its roots are in tuning cars, Brabus is now akin to a specialist car manufacturer, building a limited supply by hand. Exemplifying its engineering prowess is the completely bonkers Brabus Crawler, a 900hp monster with the essential bits from a Mercedes-AMG G63 G-Wagen (bored to 4.5-litre displacement with twin turbochargers), a steel tubular cage, Kevlar and carbon-fibre panels, carbon-racing seats and heavy-duty off-road tyres, for a 0-100kph time of 3.4 seconds — in the sand. As an interesting aside, the first of the 15 Brabus Crawlers to be built was delivered to the rapper Drake.
The Mercedes-AMG G63 G-Wagen is Brabus’ starting point for the fastest pickup truck Mercedes-Benz never built, the Brabus XLP 6X6, in 800hp and 900hp versions, with three axles, six-wheel drive, and a sawn-off G-Wagen body substituted with a pickup truck rear end.
The combination of high performance and custom detail is achieved with a panoply of high-tech machines and facilities in the factories, and skilled craftsmanship. I saw a single person restoring a classic Mercedes-Benz engine, just as a single person was assembling the electrical system of a Brabus Crawler.
classic.jpg
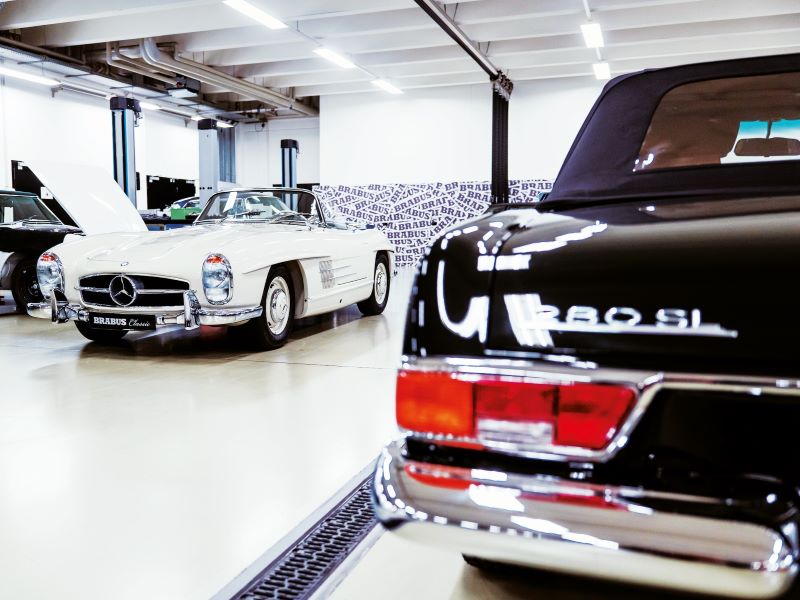
This approach extends to the interior of cars, with special machines ensuring precision cutting, sewing and piping of panels of leather hides selected by a craftsman and marked by a machine for consistent quality. Individual craftsmen see to the detailed fitting and trimming of leather panels on the seats and fascia.
A specially built configurator tool allows Brabus customers to customise and visualise their vehicles to the smallest details, from the colour of highlighting on wheels to seat piping to paint selection, body panels and so on, making each vehicle produced unique.
The imagination to build truly original — some might say, lunatic — dream vehicles, not forgetting the engineering and design expertise, skilled craftsmen and high-tech machines to develop and test the individual parts that go into each vehicle, make Brabus a master at high-performance vehicles, allowing it to construct and produce vehicles as unique to each customer as a bespoke tailored suit.
This article first appeared on Apr 22, 2024 in The Edge Malaysia.