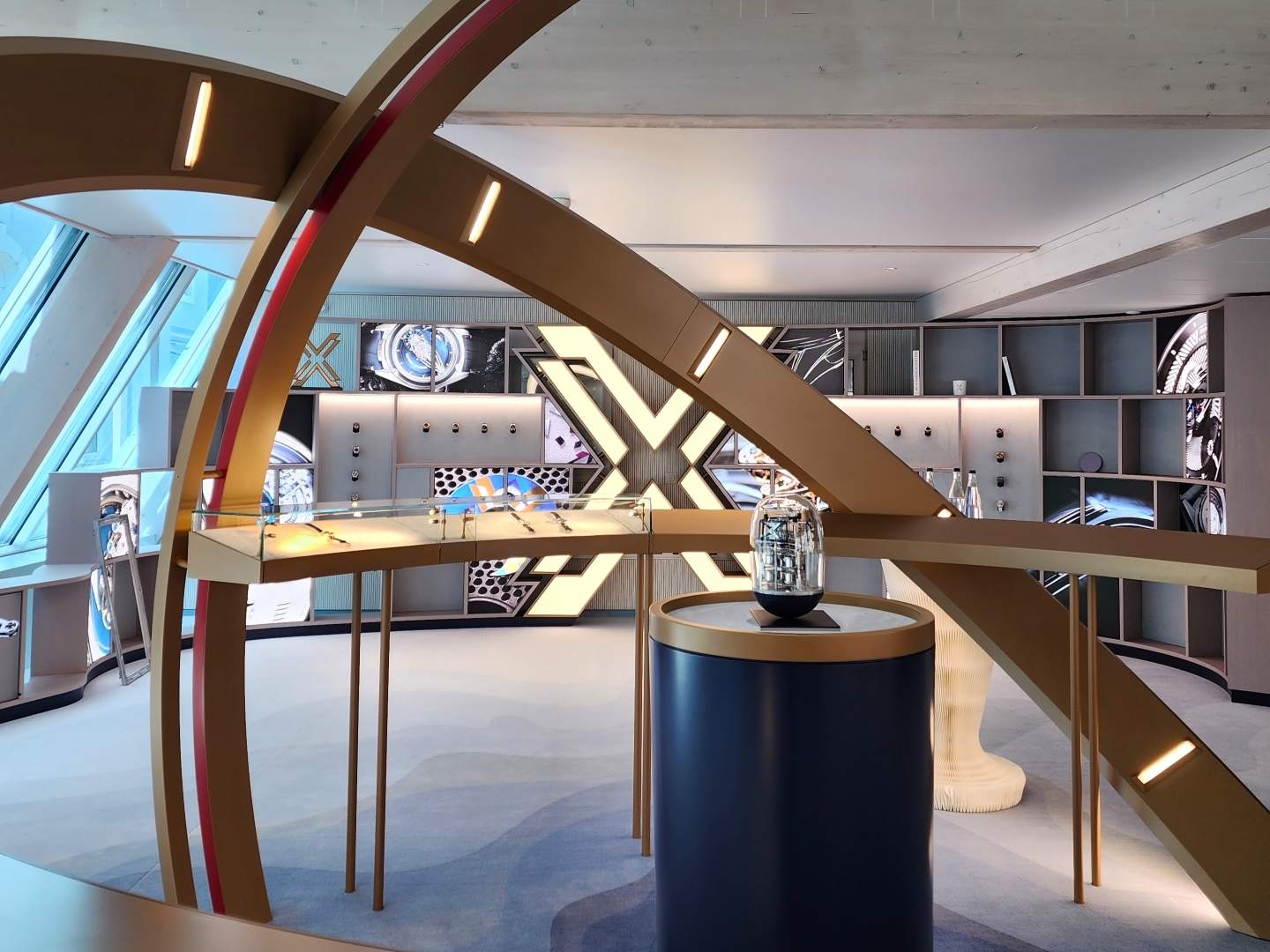
The brand has been operating out of the same historical building since 1865 (Photo: Emily Yap/ The Edge Malaysia)
The whole is often greater than the sum of its parts, but put a magnifying glass over Ulysse Nardin’s timepieces and one would see that the brilliance of each part is what makes the whole great.
The independent brand epitomises a fully integrated manufacture, with a cadre of in-house experts who produce the entire gamut, from high-precision movements and components to artistic and hand-crafted works.
Movement design, development, production and assembly are carried out at the main manufacture in La Chaux-de-Fonds, Switzerland. This is also where some of Girard-Perragaux’s components are made: It joined forces with Ulysse Nardin in a horological collective after both bid French luxury group Kering farewell last year. Despite sharing facilities, the sister brands could not be more distinct from each other, carrying with them their own unique histories — about 400 years, combined — and plans for the future.
“Ulysse Nardin is, by nature, if I may say, a manufacture, which means the cultural mindset of the company is always related to the technical content,” says chief product officer Jean Christophe Sabatier. “It is a brand of watchmakers and engineers.”
freak_one_savoir_faire_ulysse_nardin_25.jpg
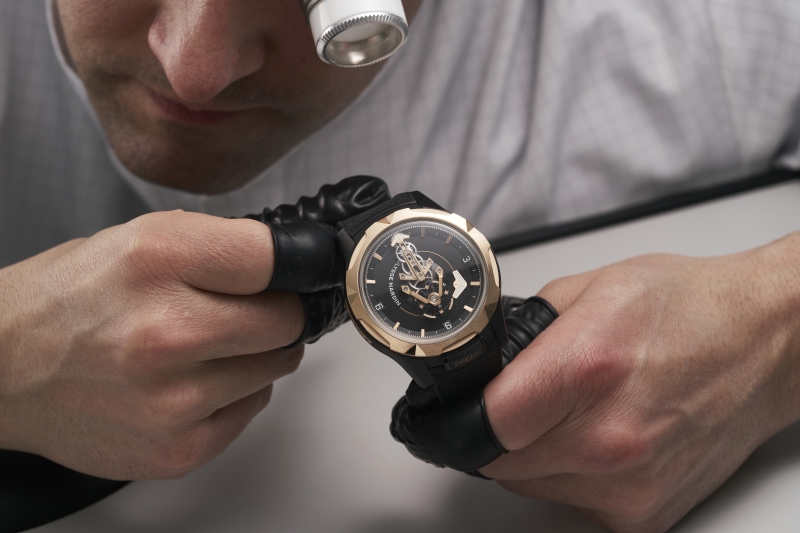
Case in point: Ulysse Nardin was the bellwether for the use of silicone before it became commonplace. It did so with the iconoclastic Freak in 2001: The watch — sans dial, hands and crown — incorporated a Dual Direct Escapement with silicone parts that resolved inertia and tolerance issues. This eventually led to a joint venture with micro-manufacturing specialist Mimotec and the subsequent establishment of Sigatec in 2006, where Ulysse Nardin’s micro-mechanical components using the light, elastic, strong and antimagnetic material would be produced moving forward.
Sigatec also produces DIAMonSIL — a patented form of diamond-coated silicone with further performance benefits — which is one of the many radical features that synthesises this year’s fantastic Freak One. And if you are keen to see how far Ulysse Nardin has progressed with the material, look no further than the Blast Free Wheel Marquetry, where the dial is adorned with 103 slivers of radiant blue silicon marquetry.
But Le Locle, the cradle of Swiss watchmaking, is where Ulysse Nardin’s headquarters stands. The brand has been operating out of the same historical building since 1865 and it is unsurprising that one would find the walls etched with didactics about its journey in aiding maritime heritage and nautical navigation. The horological cognoscenti would be chuffed to find some rare editions displayed here, including its first admiralty-type marine chronometer, one of the roly-poly-like UFOs (a modern marine chronometer) and the limited-edition (and definitely NSFW) erotic Damien Hirst timepieces.
Apart from hosting visitors, the HQ is also where the brand performs its central functions, in addition to housing a miniature painting atelier. “To understand Ulysse Nardin, it’s important to see the high-tech side of the company and then to also see the métiers d’art,” Sabatier advises. “When you visit the enamel workshop, you’ll see people working like how they did 100 years ago.”
donze_cadrans_building_1.jpg
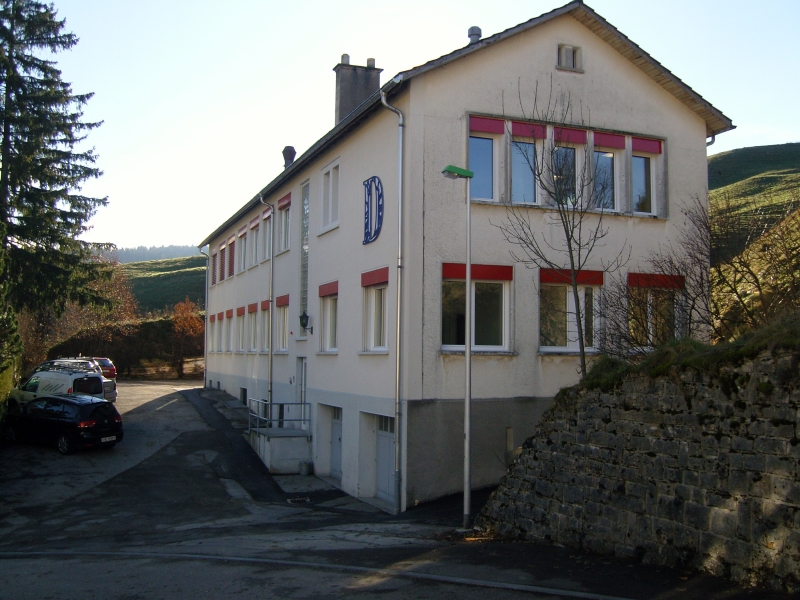
A stone’s throw from the historical building is Donzé Cadrans, founded in 1972 by master enameller Francis Donzé, who used to work with Zenith. The workshop was and still is a den of wonders. Back then, Donzé established it to preserve a rare and ancestral craft. Little did he know that his atelier would end up being one of the world’s premier sources for enamel watch dials.
His daughter and son-in-law took over the business in the 1980s while he continued his work as a craftsman. It was also around the same time that the eminent late Rolf Schnyder took up the reins of Ulysse Nardin. In 2011, Ulysse Nardin acquired Donzé Cadrans in a vertical integration, thus expanding its capabilities even further.
Donzé Cadrans is still very much an unassuming atelier, with individual work benches and stations anchored near uncurtained windows that frame the seasons’ petals, leaves and flurry that fall by the Le Locle hillside. A comfortable stillness blankets the space as deft and experienced hands work on the delicate dials using purely traditional techniques. This sort of age-old artistry, which traces back to ancient Egypt, cannot be industrialised. The most advanced equipment here are high-temperature kilns to fire the dials and microscopes that expert craftsmen and craftswomen are constantly bent over.
ulysse_nardin_donze.jpg
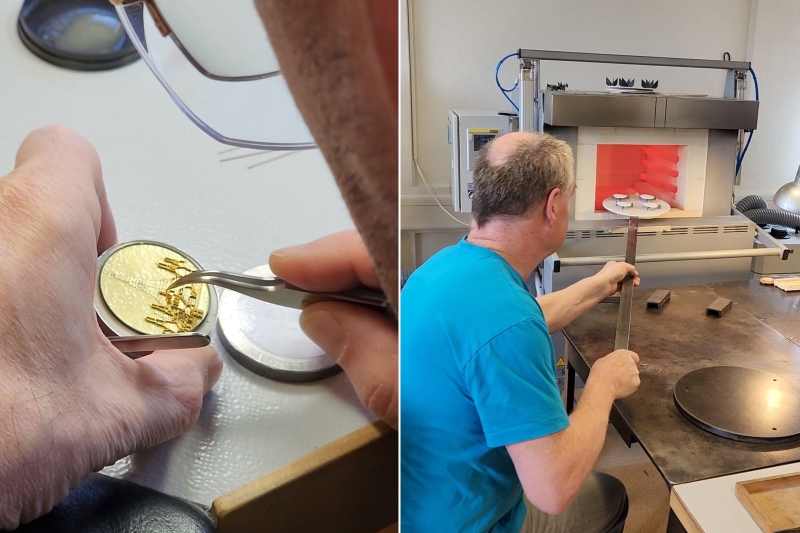
Essentially, enamel is produced through the fusion, vitrification or sintering of melted mineral compounds at temperatures upwards of 500°C. Grand feu, which translates into “great fire” in French, is the base technique used for all enamel categories at Donzé Cadrans. Using a goose quill, an enameller starts by applying an even layer of powdered glass material onto a metal base plate and fires it in the oven for the compound to melt and bond, forming a glossy surface. To achieve a saturated outcome, this process is repeated a few more times. There is a significant failure rate as enamel is naturally highly temperamental. It may crack at any stage or form bubbles and leave tiny holes — these have to be discarded. However, the reward for overcoming this protracted process is that the enamel dials retain their brilliance virtually forever.
Coloured ceramics are obtained with the addition of metal oxides to a base mixture that includes silica, minimum potash and soda. For example, selenium is added to achieve a yellow hue while chrome is used for pink and green. White, by far, is one of the most common colours, but traditionally, the key ingredient needed to achieve that sort of beautiful purity is arsenic. And to attain better ductility and lower the melting point, 20% to 40% of the mixture has to be lead. Alternatives and solutions are actively being researched to omit the potentially harmful elements.
The workshop at Donzé Cadrans employs a variety of complex techniques, some of which require close collaboration with other craftspeople. Guilloché enamel involes an engraver while flinqué enamel, a stamper. They are tasked with decorating gold or silver plates before the dials are handed to the enameller. Typically, more translucent or opalescent colours are used on these to highlight the intricate patterns underneath. A recent example of the former would be the Freak X Enamel Blue, on which geometrical lines are guillochéd onto the dial before deep blue layers of enamel are applied over several layers. This exclusive limited edition celebrates the 15th anniversary of PMT The Hour Glass in Thailand.
main.jpg
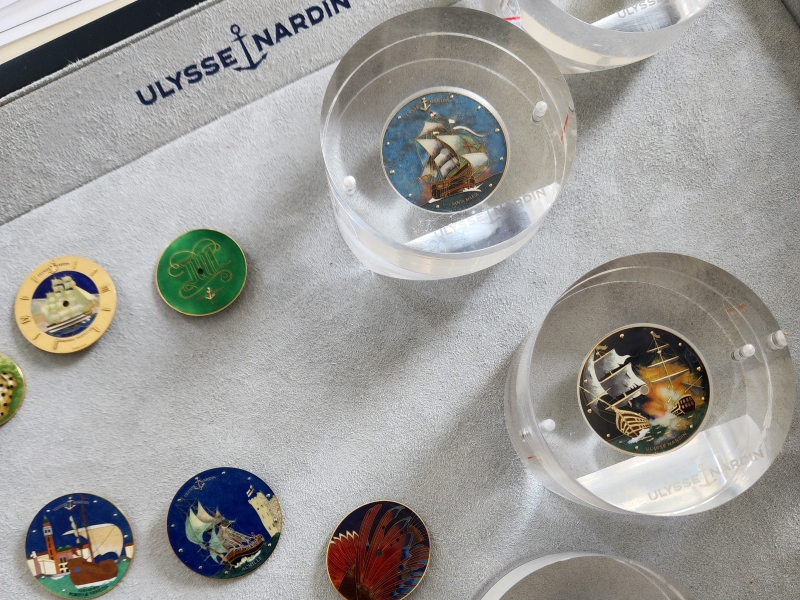
There is also the champlevé enamel, where an engraver creates pockets of cavities on a gold metal base that are filled by an enameller. The former then masterfully chisels all the excess “walls” of the various compartments to create a trompe l’oeil effect. It shares some similarities with cloisonné enamel, where gold wire is used instead to create the compartments. But because there are partitions, the enameller has to ensure an even layer on both sides so the wires do not lean during cooling. The challenge continues after the last layer is fired, as the dial will have to be drilled in order to add the appliques and the central hole. As one would expect, a miscalculation during this delicate operation would sabotage all the work done up to this point.
One reason Ulysse Nardin is able to maintain a strong foothold in the horological landscape is it equally prioritises both progression and centuries-old art forms. While the manufacture has the technological muscle to churn out outlandish timepieces like the Freak, it is also backed by artisans and craftspeople capable of making exceptional beauties, such as the new sparkling Diver Starry Night and Marine Torpilleur Moonphase Aventurine, both of which use aventurine plates, speckled with copper glitter, to mimic the vast night sky.
It begs the question: Is there anything Ulysse Nardin cannot do?
This article first appeared on Nov 6, 2023 in The Edge Malaysia.